Understanding Tungsten Inert Gas (TIG) Welding: A Comprehensive Guide
- Natalie Johnson
- Aug 20, 2024
- 3 min read
Updated: Sep 30, 2024
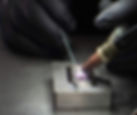
Tungsten Inert Gas (TIG) welding, also known as Gas Tungsten Arc Welding (GTAW), is a precision welding technique that uses a non-consumable tungsten electrode to create a weld. Ideal for high-quality welds on a variety of metals, TIG welding is known for producing clean, aesthetically pleasing joints. In this guide, the professionals from Micro Weld Inc. explore how TIG welding works, its key components, its applications, and how it differs from MIG welding.
Â
What is TIG Welding & How Does It Work?
TIG welding works by creating an arc between a tungsten electrode and the metal workpiece, which generates the heat necessary to melt the metal and form the weld. The electrode does not melt during the process, allowing for precise control over the weld. A shielding gas, typically argon, is used to protect the weld area from contamination and oxidation.
Â
The Tungsten Electrode
The tungsten electrode is crucial to the TIG welding process. Known for its high melting point (3422°C), tungsten withstands the intense heat generated by the arc. Unlike other welding processes where the electrode melts, the tungsten electrode remains intact, providing a stable arc and enabling high-precision welding.
Â
Filler Metal
In TIG welding, the use of filler metal is optional. When used, the filler metal is manually fed into the weld pool, which requires a high level of skill and coordination. The welder must carefully control the movement of the filler rod and the torch to avoid contaminating the tungsten electrode.
Â
Shielding Gas
Shielding gas plays a vital role in TIG welding by preventing atmospheric contamination of the weld pool. Argon is the most commonly used shielding gas due to its excellent protective qualities. In some cases, a mixture of argon and helium may be used to enhance weld penetration and speed.
Â
Applications of TIG WeldingÂ
TIG welding is widely used in industries where precision and weld quality are paramount. It's the preferred method for welding thin sections of stainless steel, aluminum, magnesium, and other exotic metals. For example, TIG welding is also common in the aerospace industry, where it’s expected to grow at a rate of 6.5% from 2020 to 2025. Additionally, it’s also frequently used in the gas and oil, and medical sectors, where precision is key.
Â
Welding Aluminum & Magnesium
TIG welding excels at welding aluminum and magnesium, metals that are challenging to weld using other processes. The alternating current (AC) feature of TIG welders is particularly effective in breaking down the oxide layer on aluminum, resulting in cleaner and stronger welds.
Â
Weld Appearance
One of the standout features of TIG welding is the clean, aesthetically pleasing appearance of the welds. Known as the "stack of dimes" look, TIG welds are smooth and require little to no post-weld cleanup, making this process ideal for projects where the weld's appearance is critical.
Â
TIG vs. MIG Welding: Key Differences
While both TIG and MIG welding are popular, they serve different purposes. TIG welding offers greater control and is ideal for high-precision work, but it requires more skill and time. MIG welding, on the other hand, is faster and easier to learn, making it suitable for general-purpose welding on thicker materials.
Â
Contact Micro Weld Inc. for TIG welding solutions and more!
TIG welding is a versatile and precise welding process that produces high-quality, aesthetically pleasing welds. While it requires a higher skill level and more time compared to other welding methods, the results are well worth the effort. Whether you're working with aluminum, stainless steel, or other exotic metals, TIG welding offers unparalleled control and precision for your projects.
Â
To learn more about precision ISO 13485-certified welding or for an estimate contact us online.